High-Density Polyethylene (HDPE) liners are widely used in environmental containment applications, including ponds, landfills, wastewater treatment, and agricultural lagoons. While HDPE is known for its chemical resistance and durability, a 20 mil (0.5 mm) thickness comes with several limitations that can affect performance and longevity.
1.Advantages of 20 Mil HDPE Liner
1.1 Significant Cost Advantage of 20mil HDPE Liner
Lower Material Costs.
Reduced Transportation and Storage Costs.
1.2 20mil HDPE Liner Easy Installation
Better Flexibility, Easier to Lay;
Higher Welding Efficiency.
1.3 Reliable Basic Impermeability of 20mil HDPE Liner
Inherent Advantages of HDPE Material.
Performs Well in Low-Stress, Smooth Environments.
1.4 Lightweight
1.5 Economical Choice for Short-Term Projects
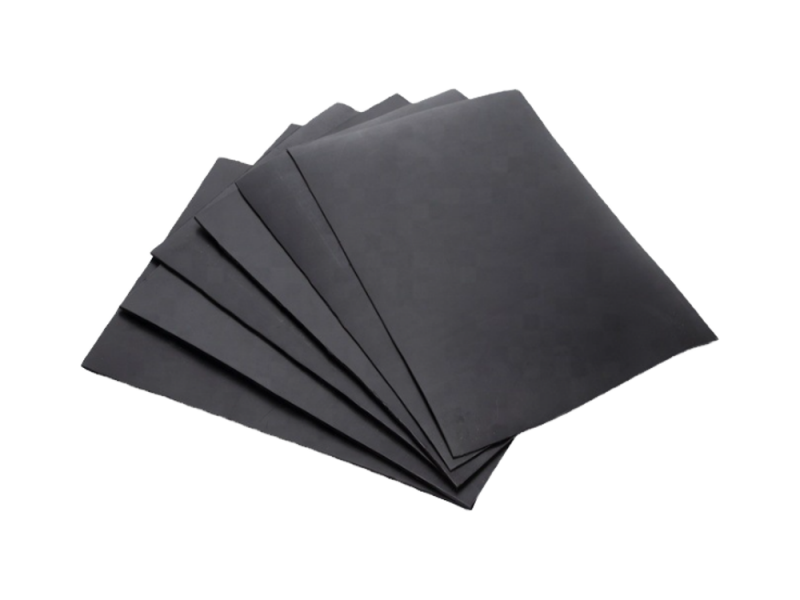
2.Drawback of 20 Mil HDPE Liner
2.1 Limited Thickness & Durability Concerns
20 mil HDPE liner is relatively thin compared to standard industrial-grade liners (typically 30–60 mil). This makes it more vulnerable to:
Punctures from sharp rocks, roots, or debris.
Abrasion damage due to foot traffic, machinery, or animal activity.
Tearing during installation or under stress.
Case Study: Agricultural Pond Failure
A farmer in Peru installed a 20 mil HDPE liner for a small irrigation pond. Within two years, cattle walking near the edges and burrowing animals caused multiple punctures, leading to leaks. The liner had to be replaced with a 40 mil HDPE liner, which provided better puncture resistance.
2.2 UV Degradation & Weathering
Unless treated with UV stabilizers, HDPE liners degrade under prolonged sunlight exposure. A 20 mil liner deteriorates faster because:
It has less material to resist UV breakdown.
Becomes brittle over time, leading to cracks and leaks.
Case Study: Temporary Containment Liner Failure
A construction site in China used a 20 mil HDPE liner for temporary chemical containment. After six months of sun exposure, the liner became brittle and cracked, allowing contaminants to seep into the soil. The project required an emergency replacement with a UV-stabilized 30 mil liner.
2.3 Thermal Expansion & Contraction Issues
HDPE expands in heat and shrinks in cold temperatures. A 20 mil liner is more prone to stress damage because:
Buckling and wrinkles develop, increasing the risk of seam failure.
Cold weather makes it stiffer, leading to cracks if not properly anchored.
Case Study: Landfill Liner Wrinkling
A municipal landfill in Colorado installed a 20 mil HDPE liner in summer. By winter, temperature fluctuations caused severe wrinkling, leading to seam separations. The liner had to be re-welded, increasing project costs.
2.4 Poor Flexibility & Conformability
Compared to LLDPE or PVC liners, HDPE is rigid, making it:
– Difficult to install on uneven surfaces.
– Prone to stress points and folds, which weaken over time.
Case Study: Lagoon Liner Leakage
A wastewater treatment plant in California used a 20 mil HDPE liner for a lagoon with a rocky base. The stiff material failed to conform to the contours, leading to gaps and leaks. The solution was switching to a **flexible 40 mil LLDPE liner**, which adapted better to the terrain.
—
2.5 Difficult Repairs & Maintenance
HDPE requires **specialized welding equipment** for repairs, unlike PVC or EPDM liners that can be patched with adhesive.
– Field repairs are costly and time-consuming.
– Small punctures can expand if not fixed properly.
Case Study: Mining Containment Repair Costs
A mining operation in Nevada used a 20 mil HDPE liner for a leaching pad. After minor equipment damage, repairs required a certified welder, causing downtime. Switching to a 30 mil reinforced liner reduced puncture risks and maintenance costs.
Lesson Learned: Thicker or reinforced liners minimize repair frequency and costs.
2.6 Chemical Resistance Limitations
While HDPE resists many chemicals, certain substances (e.g., hydrocarbons, strong oxidizers) can degrade it over time. A **20 mil liner has less material to resist permeation**.
Case Study: Fuel Storage Liner Failure
A trucking company used a 20 mil HDPE liner for secondary fuel containment. Over two years, diesel exposure caused swelling and weakening. Upgrading to a 60 mil geomembrane solved the issue.
2.7 Installation Challenges
– Requires skilled labor for heat welding.
– Poor seam welding leads to leaks.
– Wrinkles and folds increase failure risks.
Case Study: Improper Installation Leads to Leaks
A contractor in Florida installed a 20 mil HDPE pond liner but failed to properly weld seams. Within a year, leaks appeared, requiring a full replacement.
—
2.8 Environmental & Longevity Concerns
– A 20 mil liner typically lasts 10–15 years, whereas 30–60 mil liners last 20–40 years.
– Disposal is problematic since HDPE is not biodegradable.
Case Study: Landfill Liner Replacement Costs
A landfill in Pennsylvania installed a 20 mil HDPE liner to save costs. After 12 years, degradation required a full replacement, costing more than if a **30 mil liner** had been used initially.

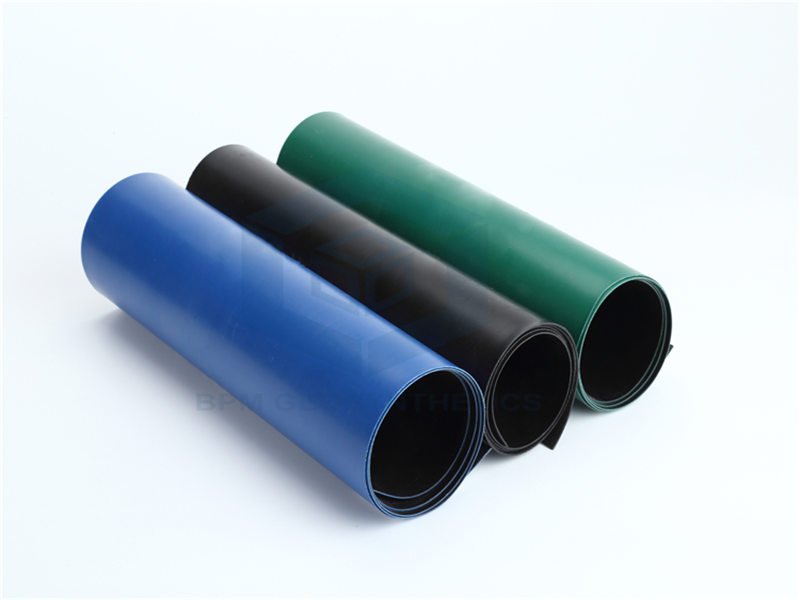