Selecting the appropriate high-density polyethylene HDPE Liner welding machine is critical to ensuring that seams in HDPE Liner installations are secure and leak-free, whether used in landfills, ponds, or mining operations. With numerous technologies and models available on the market, selecting the optimal equipment can be challenging. This guide will highlight seven key tips to help you make an informed decision, covering welding methods, material compatibility, portability, automation features, brand reliability, cost-effectiveness, and actual performance. By evaluating these critical factors, you can select the appropriate welding machine.
1. Welding Technology Types
When selecting an HDPE liner welding machine, the type of welding technology is the primary consideration. Different welding methods are suitable for different construction scenarios and directly impact weld quality and construction efficiency.
1.1 Hot Wedge Welding
Hot wedge welding is one of the most common HDPE welding techniques, particularly suitable for long-distance straight-line welding in large-scale waterproofing projects such as landfills, artificial lakes, and mines. The principle involves using an electrically heated wedge-shaped blade to melt the surface of the HDPE membrane, followed by roller pressure to fuse the material. The advantage of this method lies in its fast welding speed and high efficiency. However, it is crucial to control the heating temperature according to the construction environment, as excessive heat may cause material over-melting, while insufficient heat may result in weak welds, leading to geomembrane leaks. High-end models typically feature digital temperature control systems capable of precise adjustment within ±5°C, ensuring uniform and consistent welds.
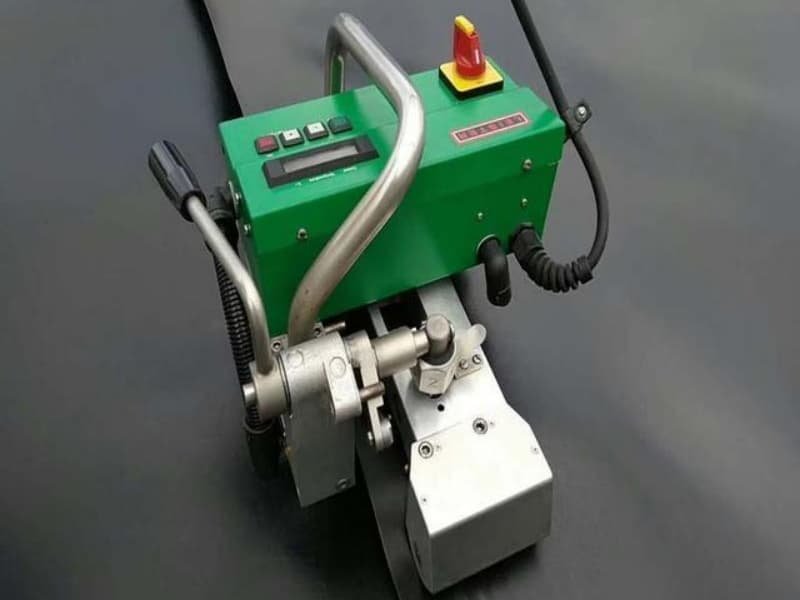
1.2 Extrusion Welding
Extrusion welding is primarily used for repairing complex shapes, corners, or T-shaped joints, such as areas where pipes penetrate or localized damage repairs. The principle involves heating and melting HDPE welding rods, then extruding them to fill the joint. This welding method offers high flexibility, but special attention must be paid to the compatibility of the extruded material to ensure that the melt flow index (MFI) of the welding rod matches that of the base material. Otherwise, it may result in poor adhesion or long-term aging and cracking. This requires a high level of welding skill from the operator.
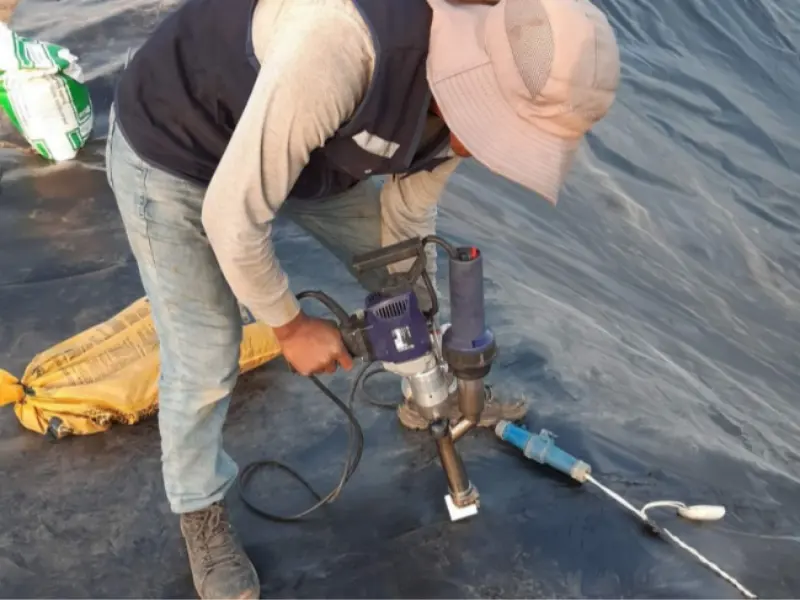
1.3 Hot Air Welding
Hot air welding is a portable welding method suitable for small-scale repairs or narrow spaces where large equipment cannot be used. It softens HDPE film with high-temperature airflow and then manually applies pressure to bond it. Although the equipment is lightweight and low-cost, special attention must be paid to airflow stability, as fluctuations in wind speed may cause local overheating or uneven welding. A high-quality hot air welder should feature adjustable airflow speed and temperature control, along with a high-quality nozzle, to ensure the weld strength meets engineering requirements.
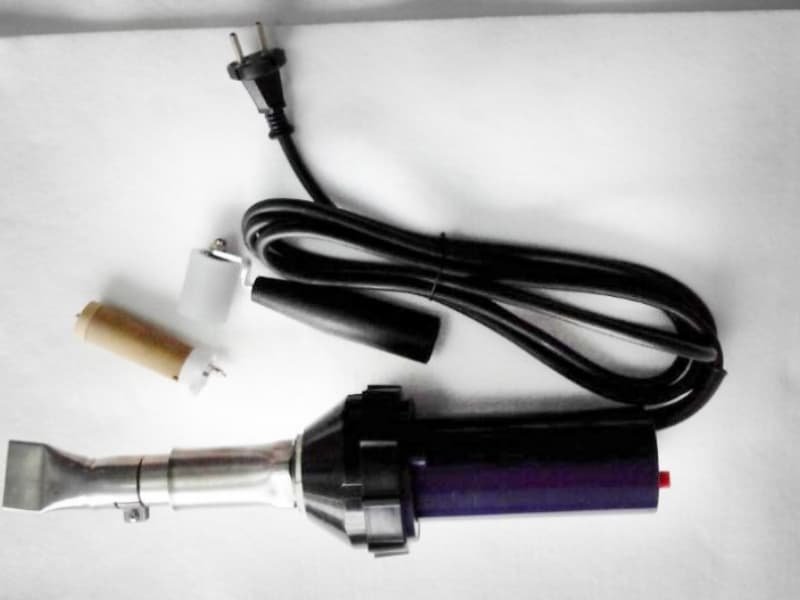
2. Material Compatibility and Thickness Range
When selecting an appropriate HDPE liner welding machine, it is essential to rigorously evaluate the equipment’s material compatibility and thickness range to ensure that the welding quality meets engineering requirements.
The thickness of HDPE liner used in different engineering projects varies, with a common range between 0.5 mm and 3 mm. The welding machine must have corresponding pressure adjustment and temperature control capabilities to accommodate materials of different thicknesses. Additionally, many projects may involve multiple types of geomembranes, such as LLDPE, PVC, or even PP membranes. Different materials have varying melting points, shrinkage rates, and chemical properties. If the welding machine is incompatible, it may result in insufficient weld strength or cracking over time. Therefore, when selecting equipment, it is important to confirm whether the device supports multi-material welding modes and is equipped with corresponding welding nozzles or temperature control programs.
3. Portability and adaptability to operating environments of welding machines
3.1 The weight and size of welding machines are key considerations.
For field work that requires frequent movement (such as reservoirs, mines, etc.), welding machines should be designed to be as lightweight as possible (recommended total weight < 15 kg) and equipped with portable moving tools. For fixed construction sites, medium to large models with wheeled stands can be selected for easy movement on rough ground.
3.2 The power adaptability of welding machines is crucial.
Standard 220V power supplies are suitable for cities or areas with grid coverage, but in remote construction sites, equipment must be compatible with diesel generator power supplies (such as supporting 110V-240V wide voltage input) and have voltage stabilization functions to prevent voltage fluctuations from affecting welding quality.
3.3 Welding machines must have a certain degree of weather resistance.
In environments with high winds, sand, and salt fog, such as deserts and coastal areas, equipment must have IP54-level dust and water resistance and use corrosion-resistant metal casings. Some high-end models also have built-in windshields to ensure that hot air welding is not affected by external air currents.
4. Automation and Precision Control
Modern geomembrane welding equipment continues to improve in terms of automation and precision control, significantly reducing human error and enhancing construction efficiency and welding quality. Equipment with automatic temperature control and speed adjustment functions can automatically adjust parameters based on different materials and environmental conditions, ensuring stable temperature and uniform travel speed during the welding process, thereby preventing issues such as overheating, incomplete welds, or burn-through caused by improper operation. Additionally, some high-end models are equipped with advanced weld quality monitoring systems, such as pressure sensors and infrared detection modules, which can monitor welding pressure and heat distribution in real time, identify defects such as bubbles, voids, or incomplete fusion in the weld, and significantly enhance construction reliability.
5. Brand Reputation and After-Sales Service
When selecting welding equipment, brand reputation and after-sales service are equally important considerations. Well-known brands such as Leister and Miller have a good reputation and extensive application cases in the industry. Their equipment usually passes multiple international quality certifications, has stable performance, and a long service life. In addition, high-quality brands generally offer longer warranty periods and have a comprehensive localized service network.
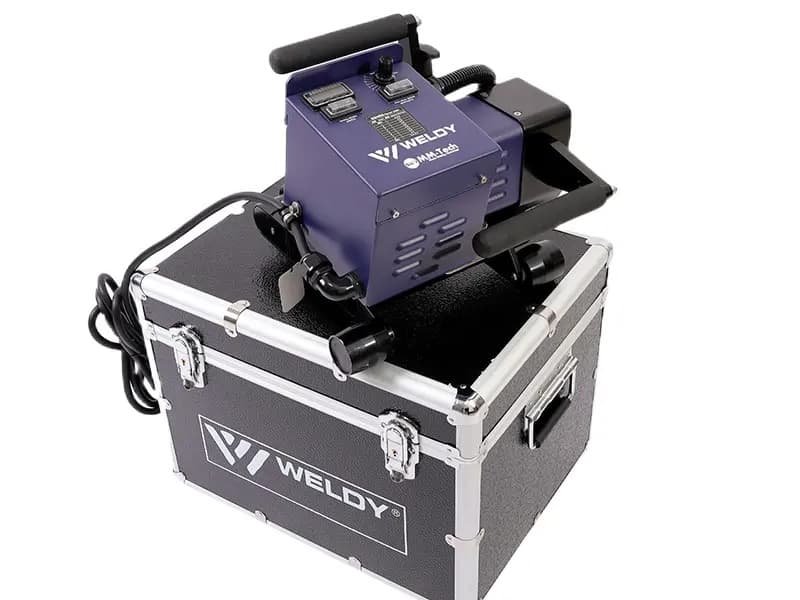
6. Cost-benefit analysis
When purchasing equipment, in addition to the initial purchase cost, it is also important to comprehensively assess the long-term maintenance costs associated with its use. For example, the price of consumables (such as heating elements and sensors) and their replacement frequency directly impact operational costs. While some equipment may have a higher initial cost, its stable performance and low maintenance frequency can make it more cost-effective over its lifecycle. For short-term projects or situations with limited budgets, leasing options can also be considered, as they reduce upfront costs while allowing access to high-performance equipment, thereby alleviating pressure on corporate cash flow.
7. User Reviews and Case References
Genuine user feedback and engineering case studies are important references for evaluating equipment performance and reliability. In large-scale projects such as landfill sites, tailings ponds, and mine seepage prevention, successful application cases can effectively demonstrate the equipment’s adaptability to different operating conditions and welding quality. Additionally, checking whether the equipment has obtained international certifications such as ISO 9001 and CE can indirectly reflect its product quality and manufacturing standards, providing strong support for procurement decisions.
8. Conclusion
Choosing the right HDPE liner welding machine requires evaluating project-specific needs, technical performance, user-friendly design, compliance standards, and future adaptability. Prioritize equipment with precision welding capabilities, ergonomic features, and proper certifications. Partnering with experienced manufacturers like The Best Project Material Co.,Ltd ensures access to customized solutions and technical support. The ideal selection balances operational requirements with long-term value, focusing on quality assurance, efficiency, and total cost of ownership for optimal project success.