Geomembrane liner, particularly high-density polyethylene (HDPE) variants, are widely used in landfills to prevent leachate leakage and protect groundwater resources. Their impermeability, chemical resistance, and relative durability make them a standard choice for containment systems. However, despite these advantages, impermeable geomembrane liners—especially those with lower thickness or specific material compositions—pose significant challenges in landfill environments. This case analysis examines the drawbacks of using such liners in landfills, including durability issues, installation complexities, environmental vulnerabilities, and long-term sustainability concerns. By dissecting these challenges, this paper aims to inform project managers, engineers, and policymakers about the trade-offs of geomembrane selection and propose alternative strategies to mitigate risks.
1. What is an Impermeable Geomembrane Liner?
An impermeable geomembrane liner is a synthetic membrane used to create a barrier against fluid migration in civil engineering projects, particularly landfills. These liners are typically made from thermoplastic polymers like HDPE, low-density polyethylene (LDPE), or polyvinyl chloride (PVC), chosen for their low permeability and chemical resistance.
1.1 Impermeable Geomembrane Liner: The Industry Standard
HDPE is the most common material for landfill liners due to its:
- Chemical Resistance: Resistance to acids, alkalis, and organic compounds present in landfill leachate.
- Durability: High tensile strength and puncture resistance compared to lighter materials.
- Thermal Stability: Ability to withstand temperature fluctuations in landfill environments.
1.2 Thickness and Performance of Impermeable Geomembrane Liner
Liner thickness is critical for landfill applications, often ranging from 1.0 to 3.0 millimeters (40 to 120 mils). Thinner liners (e.g., <1.5 mm / 60 mils) are cheaper but more susceptible to damage, while thicker liners (2.0–3.0 mm / 80–120 mils) offer superior protection but at higher cost. For context, a 30 mil (0.762 mm) HDPE liner—though not recommended for most landfills—is occasionally used in low-risk applications, highlighting the need to address its limitations.
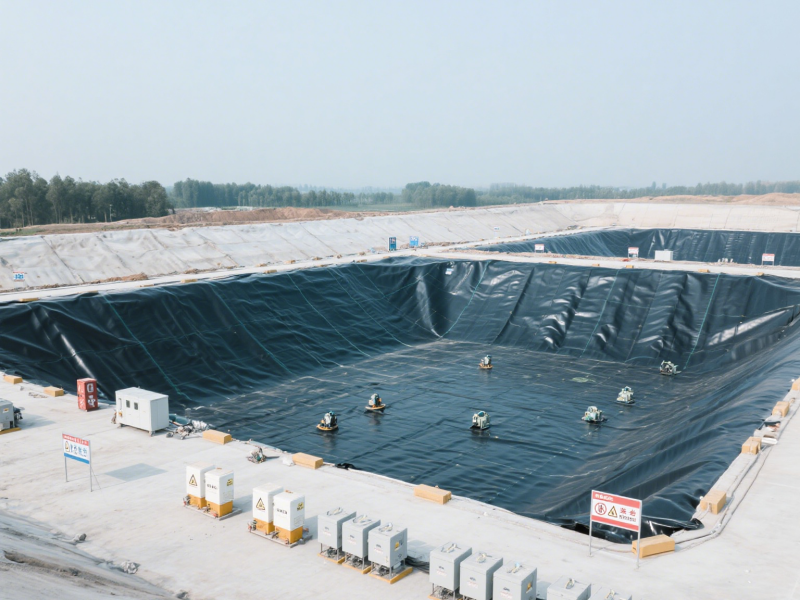
2. Why Are Impermeable Geomembrane Liners Used in Landfills?
Geomembrane liners play a pivotal role in modern landfill design, driven by the following objectives:
2.1 Prevention of Leachate Contamination
Landfill waste generates leachate—a toxic liquid containing heavy metals, pathogens, and organic pollutants. Geomembrane liners, installed at the base and slopes of landfills, act as a primary barrier to prevent leachate from infiltrating groundwater and soil. For example, in municipal solid waste (MSW) landfills, HDPE liners prevent leachate laden with ammonia, sulfides, and heavy metals from contaminating nearby water bodies.
2.2 Protection of Ecosystems and Human Health
By containing pollutants, liners safeguard surrounding ecosystems and human communities reliant on groundwater. In cases of hazardous waste landfills, where contaminants like mercury or cyanide are present, the impermeability of HDPE liners is non-negotiable for environmental safety.
2.3 Structural Stability of Impermeable Geomembrane Liner
Geomembranes enhance the structural integrity of landfill slopes by reducing erosion from rainfall and minimizing settlement-induced cracks. In engineered landfills, liners are often combined with geotextiles and drainage layers to form a multi-layered containment system, improving overall stability.
2.4 Regulatory Compliance of Impermeable Geomembrane Liner
Most environmental regulations mandate the use of impermeable liners in landfills to meet anti-pollution standards. For instance, the U.S. Environmental Protection Agency (EPA) requires municipal landfills to use HDPE liners with a minimum thickness of 1.5 mm (60 mils) to ensure long-term performance.
3. Key Disadvantages of Impermeable Geomembrane Liners in Landfills
3.1 Inadequate Durability in Harsh Landfill Environments
3.1.1 Mechanical Stress from Waste Placement
Landfills are dynamic environments where waste is compacted by heavy machinery (e.g., bulldozers, compactors), creating significant mechanical stress. Thinner liners (e.g., <1.5 mm) are prone to:
- Puncture and Tears: Sharp objects in waste (e.g., metal scraps, glass shards) can penetrate thin liners, leading to leaks. A case study in a 2018 MSW landfill in California found that 30 mil HDPE liners exhibited puncture rates 3 times higher than 120 mil liners in areas with high debris content.
- Settlement Cracks: Differential settlement of waste layers can stretch or tear liners, especially in landfills with unstable subsoil.
3.1.2 Chemical Degradation
While HDPE is chemically resistant, prolonged exposure to leachate—particularly in hazardous waste landfills—can cause slow degradation. For example:
- Solvent Attack: Certain organic solvents in industrial waste can plasticize HDPE, reducing its tensile strength over time.
Microbial Activity: Anaerobic bacteria in landfills produce organic acids that may weaken liner .
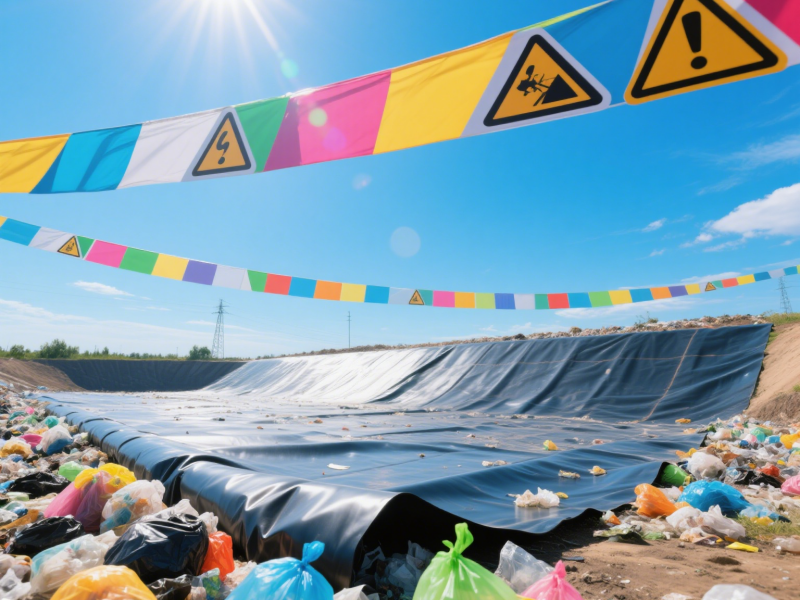
3.2 Installation Complexity and Human Error
3.2.1 Challenges with Uneven Subgrade
Landfill subgrades often have irregular topography or hidden obstacles (e.g., rocks, roots). Thinner liners (e.g., 30 mil HDPE) lack the rigidity to conform to uneven surfaces, leading to:
- Wrinkles and Air Pockets: Inadequate tension during installation can create folds that trap gas or water, compromising barrier integrity.
- Incomplete Welding: Thin liners require precise heat welding, and even minor gaps in seams (e.g., 0.5 mm misalignment) can create leakage pathways. A 2020 study in a European landfill found that 30% of welding defects in 60 mil liners were due to operator error during thermal fusion.
3.2.2 Weather-Dependent Installation
Extreme temperatures hinder liner installation:
- Old Climates: HDPE becomes brittle at low temperatures, increasing the risk of cracking during handling or welding.
- Hot Climates: Excessive heat can cause liners to expand, leading to slack or uneven tension when cooled.
3.3 Poor UV Resistance and Long-Term Aging
3.3.1 Ultraviolet Degradation
During construction, liners may be temporarily exposed to sunlight before waste placement. UV radiation breaks down polymer chains in HDPE, causing:
- Brittleness: Prolonged UV exposure (e.g., >3 months) can reduce elongation at break by 50%, making liners more prone to cracking.
- Surface Chalking: A visible sign of degradation, where the liner’s surface becomes powdery and loses flexibility.
3.3.2 Long-Term Aging Mechanisms
Even buried liners degrade over time due to:
- Oxidative Stress: Reactive oxygen species from waste decomposition accelerate polymer oxidation, reducing tensile strength by ~2% per decade (ASTM D4355 standards).
- Thermal Cycling: Seasonal temperature changes cause liners to expand and contract, leading to fatigue cracks over 10–20 years.
3.4 Environmental and Sustainability Concerns
3.4.1 Non-Biodegradable Waste
HDPE liners are non-biodegradable, contributing to plastic pollution at end-of-life. When landfills are closed or expanded, removed liners often end up in new landfills, perpetuating waste cycles. In the EU, only ~15% of geomembranes are recycled, with the rest incinerated or landfilled.
3.4.2 High Carbon Footprint
Producing HDPE requires significant energy: ~3–5 tons of CO₂ emissions per ton of HDPE. Thicker liners (e.g., 120 mil) have a 4x higher carbon footprint than thinner variants, contradicting sustainability goals in circular economy initiatives.
3.4.3 Microplastic Release
Abrasion from waste or machinery can shed microplastics from liners, which may enter groundwater or the food chain. A 2022 study detected HDPE microplastics in leachate samples from 80% of landfills surveyed, raising concerns about long-term ecological impacts.
3.5 Cost Implications
While thinner liners (e.g., 30 mil) have lower upfront costs, lifecycle costs often escalate due to:
- Repair Costs: Leak detection and repair in landfills can cost 2–5 times the initial liner installation cost.
- Early Replacement: Thin liners may need replacement after 10–15 years, compared to 25–30 years for thicker liners, increasing long-term expenditure.
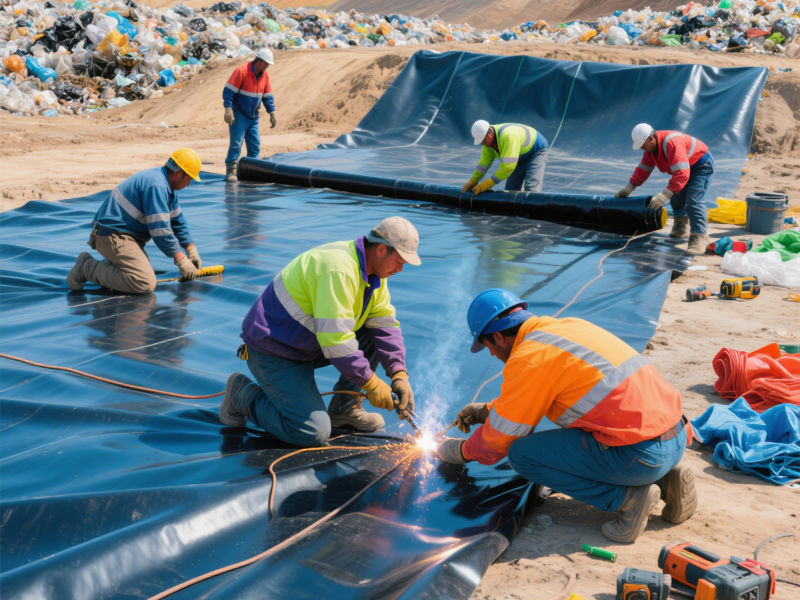
4. Mitigation Strategies and Alternatives
To address these disadvantages, stakeholders can adopt the following approaches:
4.1 Material Upgrades
- Thicker Liners: Use 1.5–3.0 mm (60–120 mil) HDPE liners for high-risk landfills, prioritizing puncture resistance and durability.
- Reinforced Geomembranes: Incorporate polyester or polypropylene grids into liners to enhance tensile strength and reduce stretching.
4.2 Improved Installation Practices
- Subgrade Preparation: Conduct thorough site surveys to remove sharp objects and level the base.
- Quality Control: Use non-destructive testing (e.g., vacuum box tests,电火花 testing) to verify weld integrity.
- Climate-Adaptive Installation: Schedule installation during moderate temperatures and avoid prolonged UV exposure.
4.3 Sustainable Alternatives
- Biodegradable Liners: Explore bio-based polymers like poly(lactic acid) (PLA) or starch-based composites for low-risk applications, though these are still in developmental stages.
- Geosynthetic Clay Liners (GCLs): Combine geomembranes with GCLs for a dual-barrier system, enhancing seepage control and reducing reliance on thick HDPE.
4.4 End-of-Life Management
- Recycling Initiatives: Promote post-consumer recycling of HDPE liners through industrial partnerships.
- Energy Recovery: Incinerate liners in energy-from-waste facilities to generate electricity, reducing landfill dependence.
5. Conclusion
Impermeable geomembrane liners, while essential for landfill containment, are not without flaws. Their susceptibility to mechanical damage, installation challenges, UV degradation, and environmental impacts necessitate careful material selection and proactive risk management. For high-stakes landfills (e.g., hazardous waste, large MSW sites), investing in thicker, reinforced liners and robust installation protocols is critical to avoid costly failures and environmental harm.
As the industry evolves, embracing sustainable alternatives and circular economy principles—such as recyclable liners and dual-barrier systems—will be key to balancing functionality with ecological responsibility. By addressing these disadvantages head-on, landfill operators can enhance safety, comply with stricter regulations, and contribute to a more sustainable waste management future.
- Note:
For customized geomembrane solutions that mitigate these risks, BMP—a leading geosynthetic manufacturer—offers engineered HDPE liners with enhanced puncture resistance, on-site installation support, and lifecycle sustainability planning. Contact our team to design a liner system tailored to your landfill’s unique needs.